Types of welding: Basically welding may be classified into three types. Plastic welding: In plastic welding or pressure welding process, the pieces of metal to be joined are heated to a plastic state and then forced together by external pressure. These welding are also known as liquid-solid welding process.
Welding is a process of permanently joining two or more parts by the application of heat and (or) pressure. As per American Welding Society 50 different welding processes available today; some are very popular among the industries such as SMAW, GMAW, GTAW, SAW, FCAW etc. Whereas some are very specific and limited to few industries such as USW, RSW, DW etc.Welding processes are broadly classified as fusion welding and solid state welding;FUSION WELDING: In Fusion welding coalescence is done by melting the base metals by the application of heat. Required heat is generated by an electric arc formed between the electrode and the workpiece. Very often filler metal is also used. Commonly used fusion welding processes are:.
Arc Welding. Carbon Arc Welding. Stud Welding2. Resistance Welding. Resistance Spot Welding. Resistance Seam Welding. Resistance Projection Welding.
Gsa captcha breaker cracked. GSA Captcha Breaker Breaks any Captcha - Works with any Software. This software will break almost any captcha type for you and integrates into any software that uses captcha services to solve them. No need to pay for captcha solving ever again, let this software handle it all for you. Comes with an editor to add new captcha types.
Flash Welding3.4. Others.
Electron beam welding. Laser beam WeldingSOLID STATE WELDING: In solid state welding, joining is done by the application of pressure alone or a combination of pressure and heat. Normally the base metal is not reached to the melting point, if heat is applied to obtain the coalescence and filler metal is not used. Some of the solid state welding processes are:. Diffusion welding (DFW).
Friction welding (FRW). Ultrasonic welding (USW). Cold Welding.
Types Of Welding Process Pdf
Forge welding. Explosion welding (EXW)In the following video, I have simplified the different welding processes and categorized for your easy understanding. Please watch this video and share your views as well as queries. I will be glad to answer your queries.
Here we discover the different types of welding joints and the types of welding styles used to create each.The ‘s (AWS) definition of a joint is “ the manner in which materials fit together“.The applications of welding are limitless. From the aeronautic industry to automotive and residential its applications and critical roll cannot be understated. It is a practical solution that provides superior strength that many of us bet our lives on to function and hold under strain. These welds offer low weight, high strength, rigidity, and lower cost in production.Table Of Contents. Tee Welding JointTee JointTee welding joints are formed when two members intersect at a 90° angle which makes the edges come together in the center of a plate or component. Tee Joints are considered a type of fillet weld, and can also be made when a pipe or tube is welded onto a base plate.
Extra care is required to ensure effective penetration into the roof of the weld.Welding Styles Used To Create T-Joints. Plug weld. Fillet weld.
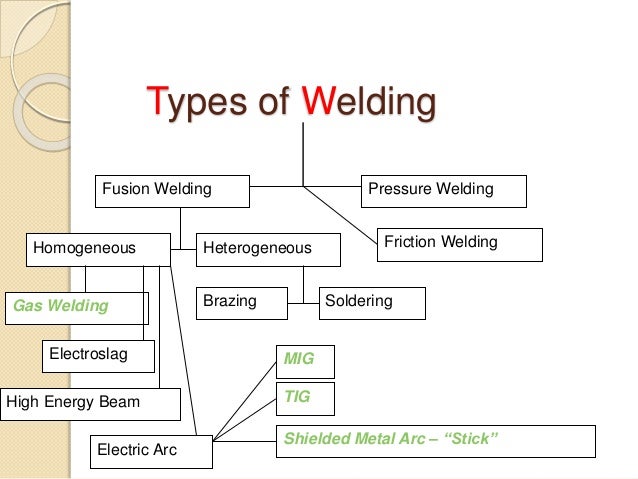
Bevel-groove weld. Slot weld. Flare-bevel-groove weld.
J-groove weld. Melt-through weld. Edge Welding JointEdge JointEdge welding Joints are often applied to sheet metal parts that have flanging edges or are placed at a location where a weld must be made to attach to adjacent pieces. Being a groove type weld, Edge Joints, the pieces are set side by side and welded on the same edge.
For heavier applications filler metal is added to melt or fuse the edge completely and to reinforce the plate.Welding Styles Used To Create Edge Joints:. Bevel-groove weld. Square-groove weld or butt weld.
J-groove weld. V-groove weld. Edge-flange weld. U-groove weld. Corner-flange weld.
Corner Welding JointCorner JointBeing one of the most popular welds in the sheet metal industry the Corner welding joint is used on the outer edge of the piece. This weld is a type of joint that comes together at right angles between two metal parts to form an L. These are common in the construction of boxes, box frames and similar fabrications.Welding Styles Used To Create Corner Joints:. Spot weld. Fillet weld.
V-groove weld. Square-groove weld or butt weld. U-groove weld. Bevel-groove weld. Flare-V-groove weld.
J-groove weld. Corner-flange weld. Edge weld. Butt Welding JointButt JointBeing the universally accepted method for attaching a pipe to itself it’s also used for valves, flanges, fittings, and other equipment. A butt welding joint is also known as a square grove weld.
It’s the easiest and probably the most common weld there is. It consists of two flat pieces that are side by side parallel. It’s a very affordable option.Welding Styles Used To Create Butt Joints:. Bevel-groove butt weld. Square-groove butt weld. V-groove butt weld.
U-groove butt weld. J-groove butt weld. Flare-bevel-groove butt weld. Flare-V-groove butt weld. Fillet Welding JointFillet Welded JointsFillet Welded Joints are just another terminology for corner, lap, and tee joints. Fillet Welded Joints are the most common type of welding joint and accounts for nearly 75% of joints made with arc welding.
You do not need to prepare the edge and this type of joint make it easy to weld piping systems. Butt welds are more expensive than fillet welds. Fillet welds are mostly used in piping systems to join pipe to socket joints. Joint PreparationWelding joints can be prepared in numerous ways including:. Casting. Shearing. Machining.
Forging. Filing. Stamping. Oxyacetylene cutting (thermal cutting process). Routing. Grinding. Plasma arc cutting (thermal cutting process)A Brief Word On Welding SafetyIf you’re just learning or even if you’ve done welding for years it can’t be said enough that it’s critical to be fully aware of your surroundings when you begin to weld.
You must take the time to know who’s around trying to watch and what dangers you are exposing yourself to. Welding vs RivetingWelding and riveting are two ways to join metal to metal. They both have their particular pros and cons. Different situations call for one or the other.
Neither is best for every possible situation. We’ll take a look at the different strengths and weaknesses of both metal joining systems.

Ways Welding Is Better Than Riveting. Welding can be done anywhere on the structure. Edges can be welded to edges without having to overlap. Riveting needs to have a certain amount of clearance from the edges to be joined. Welding saves weight in the construction process.
Since metal is actually joined to metal, gussets or other connecting hardware is not needed. Even the rivets themselves have weight, so being able to join the metal together without having to use them saves a bunch of weight. Unlike riveted joints the tensions members’ strength is not diminished by welding. Quality welding leaves a smooth surface, while riveting has the ends of rivets on the surface of the whole structure.
Using welding to produce a strong yet beautifully smooth surface creates our functional but aesthetically pleasing architecture. Welded joints are better many times because the material on both sides of the weld is actually physically joined. Welding can easily join sections of metal column or pipe. Trying to join these items with rivets can be difficult or impossible given certain situations. Welding is a faster way of joining metal. This means that is you have a time sensitive project welding holds the edge.
It also means less man hours, which helps save on costs. Additions or alterations can easily be made with welding. Structures built with rivets are less flexible and additional engineering is necessary to make these changes with riveting.Need Welding Services In Mesa, Arizona?Why not leave it to the professionals at? You will be able to rest assured that the pros have handled your job, big or small to the correct standards and codes to ensure the durability and strength of the welds.Give us a call at or use our.Thank you for visiting “ Types Of Welding Joints” post. Stay tuned for more from Cliff’s Welding.